Nagamohr es una empresa especializada en decoletaje de precisión, fundada en 1993 tras el traslado de un pequeño centro de producción de Alemania a España. Desde entonces, ha crecido significativamente y ahora cuenta con más de 150 empleados
La empresa se dedica principalmente a la producción de ejes de precisión para la industria del automóvil, y tiene capacidad para producir grandes series, utilizando tecnología avanzada para garantizar la alta calidad de sus productos. Fabrica, entre otros productos, diferentes tipos de ejes como:
Ejes de transmisión macizos y huecos
Ejes para motores eléctricos
Ejes para cajas de distribución
Ejes y válvulas para sistemas de recirculación de gases.
Estos ejes se utilizan en sistemas como limpiaparabrisas, elevalunas eléctricos, asientos ajustables motorizados, techos solares, cajas de distribución y sistemas de escape.
Para asegurar que el 100% de sus piezas cumplen con los requisitos de calidad de sus clientes, dispone de sistemas automatizados de control de calidad que incluyen sofisticados equipos de control dimensional mediante visión artificial, láser, comparadores electrónicos y detección de defectos superficiales como grietas y poros, mediante corrientes inducidas. Recientemente ha integrado un control de dureza, tratamiento térmico y diferencias de aleación también mediante corrientes inducidas.
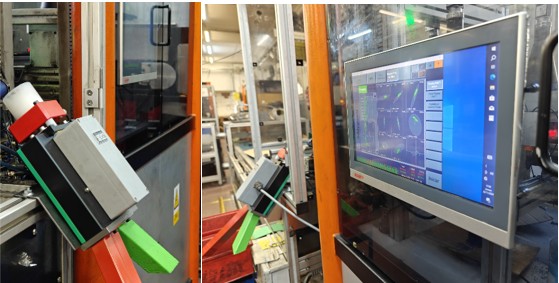
El control de dureza está compuesto por un eddyguard S de IBG, bobinas circunferenciales y un Unisort para clasificar las piezas una vez inspeccionadas y rechazar las piezas que no tengan la dureza correcta, un tratamiento térmico defectuoso o un material equivocado. El sistema se pudo integrar de forma sencilla en una máquina ya existente, fabricada por MCV (https://www.mcvision.es/ ) sin tener que modificar el tiempo de ciclo, que es menos de 2 segundos por pieza. Con este equipo multifrecuencia, que trabaja tanto con frecuencias fundamentales como con 2 familias de armónicos, es posible, no solo detectar piezas que no han recibido el tratamiento térmico, sino que se detectan piezas con una dureza incorrecta con diferencias de hasta 15-20 HV10.
Las piezas son inspeccionadas por visión artificial mediante cámaras para verificar multitud de cotas y tras este primer test, las piezas caen por una rampa donde tenemos colocada la bobina que en cuestión de milisegundos chequea la dureza y la correcta aleación para luego, mediante el clasificador Unisort 25, separa las piezas correctas de las NOK.
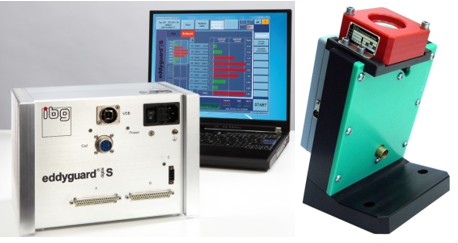
Para la puesta en marcha se utilizaron las siguientes piezas:
Piezas OK tratadas y con durezas de 400-440 HV10 para el ajuste del equipo.
Piezas sin tratar con durezas de 230-255 HV10
Piezas NOK con durezas de 203-210 HV10
Piezas tratadas con durezas de 370-380 HV10 (en el límite) Utilizamos la siguiente configuración, con 8 frecuencias que van de 25 Hz a 25 k Hz con un tiempo de inspección de 240 ms teniendo un retraso de inicio de 100ms, lo que implica que la inspección se lleva a cabo en140 ms.
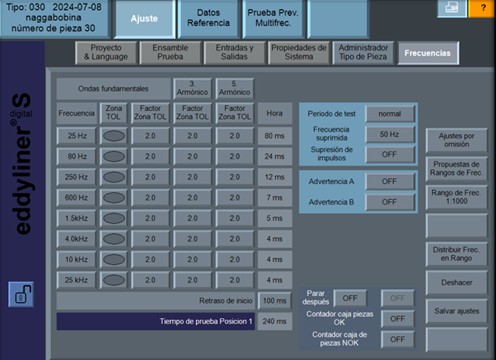
Piezas 4, 5 y 6 se rechazan en la tercera familia de armónicos por muy poco, pero son piezas de 378 a 385 HV10.
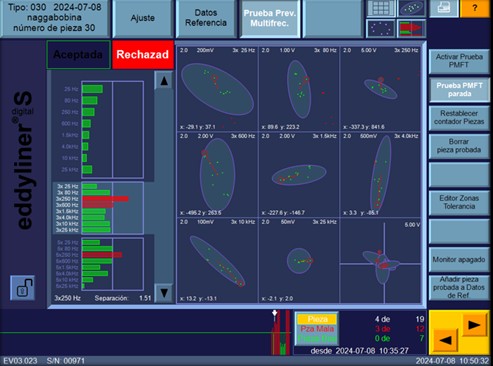
Las piezas no tratadas con durezas de 203-210 HV10 se rechazan con valores de 20.
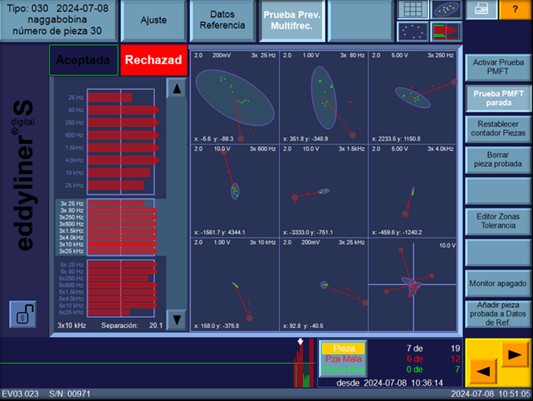
Piezas con durezas de 230-255 HV10 son rechazadas en el 3er armónico con valores de 7.
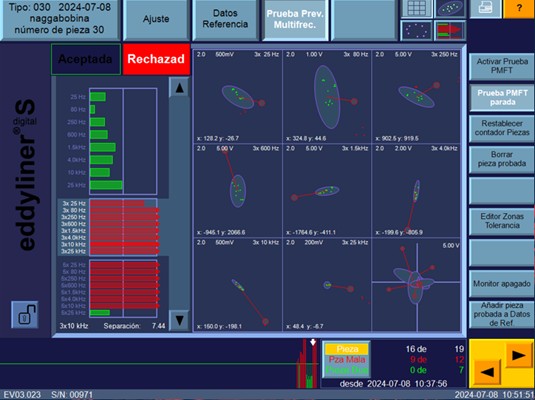
Gracias a la implementación de este sistema de corrientes inducidas, Nagamhor no solo controla dimensionalmente el 100% de las piezas procesadas, ahora puede garantizar que sus clientes reciben piezas con el rango de dureza correcto.
Además, el sistema se pudo integrar en una máquina ya existente sin necesidad de tenerla parada más de unas horas, sin necesidad de grandes modificaciones, y manteniendo el tiempo de ciclo necesario.
Desde FDNDT queremos agradecer a todo el equipo de Nagamhor la confianza en nosotros y nuestras soluciones.
Si necesitas que te ayudemos a controlar el tratamiento térmico o dureza de tus piezas no dudes en ponerte en contacto con nosotros, estudiaremos tus necesidades y buscaremos la mejor solución.