Una de las aplicaciones más usadas y extendidas de las corrientes inducidas es el control de la producción en piezas de automoción. El objetivo es verificar una correcta estructura o aleación, la dureza, un correcto tratamiento térmico o bien la profundidad de capa templada.
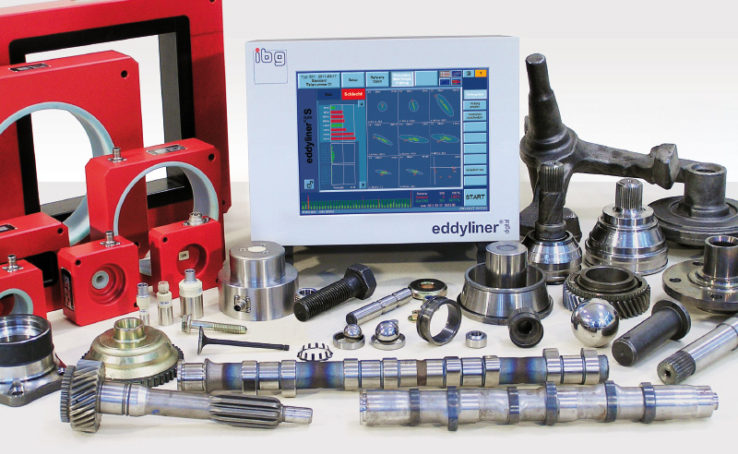
Equipo Eddyliner S con accesorios de IBG con ejemplos de piezas inspeccionadas.
FD NDT lleva años proporcionando soluciones a los fabricantes de piezas de automoción que les permitan controlar el 100% de sus piezas producidas, cumpliendo así con los estándares de calidad actuales en este sector.
Nuestras soluciones abarcan desde estaciones manuales o semiautomáticas, hasta instalaciones completamente automatizadas, ya sea en línea, en estaciones independientes, o bien integradas en máquinas de control de calidad ya existentes que utilizan otras tecnologías como pueden ser sistemas de visión artificial.
Hay muchas maneras de efectuar este tipo de ensayos, se puede hacer en estático, es decir, parando la pieza para inspeccionarla, o en dinámico, inspeccionando la pieza en movimiento, ya sea en una cinta transportadora o en una mesa rotativa. Utilizando bobinas, ya sean circulares, rectangulares, abiertas, bobinas interiores o bien con sondas.
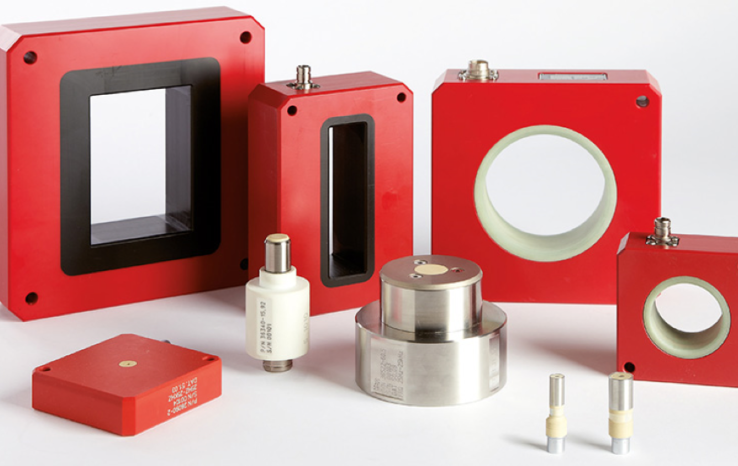
Algunos ejemplos de bobinas y sondas de la firma IBG
La elección dependerá de muchos factores como, por ejemplo:
Tiempos de ciclos:
Con un test dinámico podemos inspeccionar un número mayor de piezas que con un test estático, pero por contra se suele perder sensibilidad o poder de detección en un test dinámico. Con un test estático podemos tener velocidades de inspección de 1 a 1,5 piezas segundo con un canal (pudiendo aumentar la velocidad añadiendo canales de inspección en paralelo), mientras con un test dinámico podemos inspeccionar a velocidades de 10 piezas segundo o más.
Sensibilidad de detección:
Dependiendo del tipo de defectos que queramos detectar utilizaremos bobinas circulares o rectangulares, abiertas, interiores o sondas. Las bobinas circulares y rectangulares suelen tener más sensibilidad pudiendo detectar diferencias más pequeñas de material o dureza (de hasta 3-5 HRC), mientras que las bobinas abiertas o sondas no tendrían la sensibilidad de detectar pequeñas diferencias. También influye en la sensibilidad el tamaño de la pieza respecto al de la bobina, cuanto más se acerque el tamaño de la pieza al de la bobina utilizada mejor sensibilidad tendremos.
Tipo de pieza:
dependiendo de la geometría de la pieza puede ser más adecuado el uso de una sonda o una bobina envolvente, abierta o una bobina interior, igualmente, si toda la pieza tiene la misma estructura/dureza posiblemente utilicemos una bobina mientras que si la misma pieza puede tener zonas de diferentes durezas o aleación utilizaremos una sonda y tomaremos diferentes medidas en la misma pieza, pudiendo discriminar no solo piezas de diferente estructura sino también piezas que tengan áreas o zonas de diferente estructura.
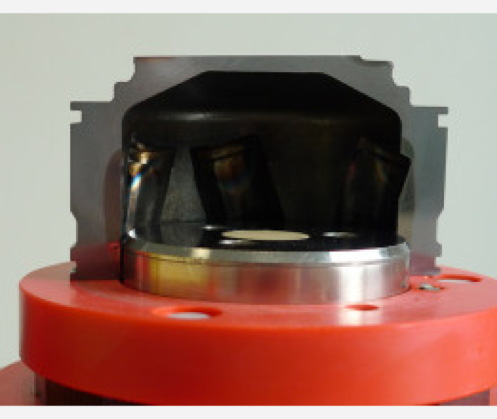
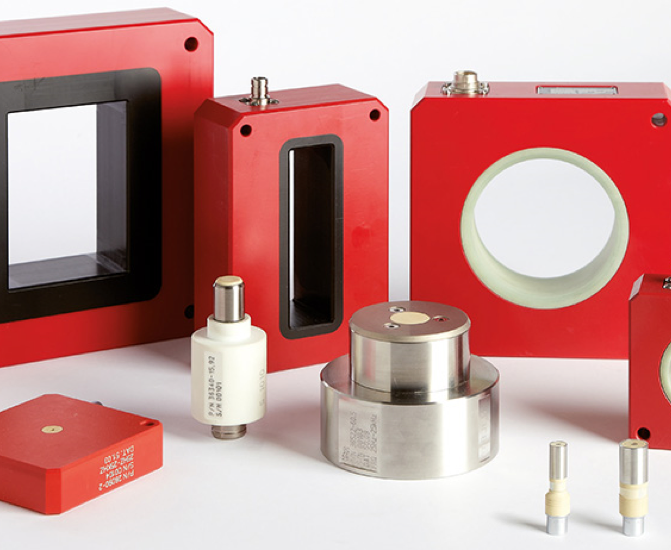
Foto 1: Foto de bobina ID para control del temple zona interior, en este caso se puede ver como la zona templada está desplazada lo cual generaría una señal de NO OK y la pieza sería rechazada.
Foto 2: Gama de bobinas abiertas de IBG
Máquina o línea donde ha de ir instalado el control:
el lugar donde hemos de integrar el equipo también nos puede obligar a utilizar un tipo de sensor u otro, normalmente un plato rotativo implicará la utilización de una bobina abierta o una sonda, mientras que en una cinta transportadora podemos utilizar una sonda o una bobina rectangular (haciendo pasar la cinta por dentro de la bobina).
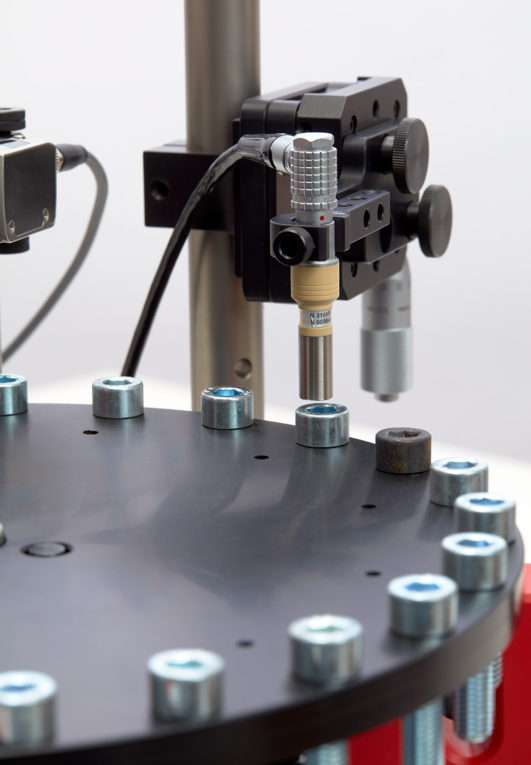
Inspección dinámica en plato rotativo con diferentes opciones de bobinas y sondas.
Inspección dinámica en cinta transportadora con sonda de rodillos de rodamientos de nuestro cliente Fersa. El video fue grabado durante unas pruebas de viabilidad hechas en IBG.
Una misma pieza puede inspeccionarse de diferentes maneras dependiendo de la tipología de defecto, nivel de automatización, tipo de integración o velocidades de inspección entre otros factores.
En FD NDT siempre aconsejamos hacer un estudio previo de viabilidad para verificar que la solución cumple con los requisitos del cliente, analizar primero que tipo de sensor o sensores son capaces de detectar los defectos para luego ver como los integramos en la línea de producción o máquina de verificación del cliente.
Algunos ejemplos de aplicaciones que hemos llevado a cabo durante los últimos años:
· Control de verificación estructura Ferrítica- Perlítica (max. 25% de Perlita) en piezas de fundición sector automoción.
· Control presencia Cementita en piezas de fundición sector automoción.
· Control del correcto temple por inducción integrado en la máquina de temple en tulipas y otros elementos de transmisión del sector automoción. Pudiendo discriminar entre pieza templada o no templado o también detectar piezas con la zona templada desplazada, o una profundidad de la capa templada incorrecta (demasiada profundidad o profundidad insuficiente)
· Control de dureza/tratamiento térmico en piezas sinterizadas.
· Control de dureza/tratamiento térmico en rodillos, agujas y bolas de rodamientos.
· Control de dureza/tratamiento térmico en tornillos, tuercas y diversos elementos de fijación integrados en máquinas de visión artificial.
· Control de dureza/tratamiento térmico en tuercas sector automoción integrado en máquina de visión artificial.
· Control de profundidad de capa en tratamiento de nitro carburación en engranajes de caja de cambio automoción.
· Control de dureza/temple inducción en vástagos de amortiguadores.
· Control de dureza/tratamiento térmico en piezas de seguridad de corte fino.
· Control de dureza/tratamiento térmico en piezas de estampación.
· Control de dureza/tratamiento térmico en piezas de forja.
· Control de mezcla de materiales en barras previas al proceso de forja.
Y para acabar un par de aplicaciones curiosas en las que además de utilizar el equipo de Corrientes inducidas para control de estructura se utilizaba para:
· Control de posición de piezas asimétricas. El equipo de corrientes inducidas estaba situado justo antes de meter la pieza en la rectificadora, y además de controlar la estructura y dureza, se aseguraba que ésta estaba bien orientada para introducir en la rectificadora el lado correcto.
· Control de centrado de mecanizado. En este caso una empresa de mecanizado de pequeñas piezas utilizaba el equipo de corrientes inducidas para, además de controlar la estructura /dureza de las piezas, verificar que un mecanizado interno estaba bien centrado en la pieza, en aquellas piezas en las que el mecanizado interno no era el correcto se generaba una pared con muy poco espesor y generaba una señal de NO OK rechazando toda pieza con el mecanizado descentrado.
Si estas interesado en conocer más a fondo nuestras soluciones o necesitas que te asesoremos acerca de la mejor opción de controlar el 100% de tus piezas no dudes en contactarnos.